Breaking Down Different Types of Technical Documentation
- Scriptorium Team
- Dec 18, 2024
- 4 min read
Warning! We are entering a jargon-laden blog, but Scriptorium is here to help you walk through this field of technical terminology.
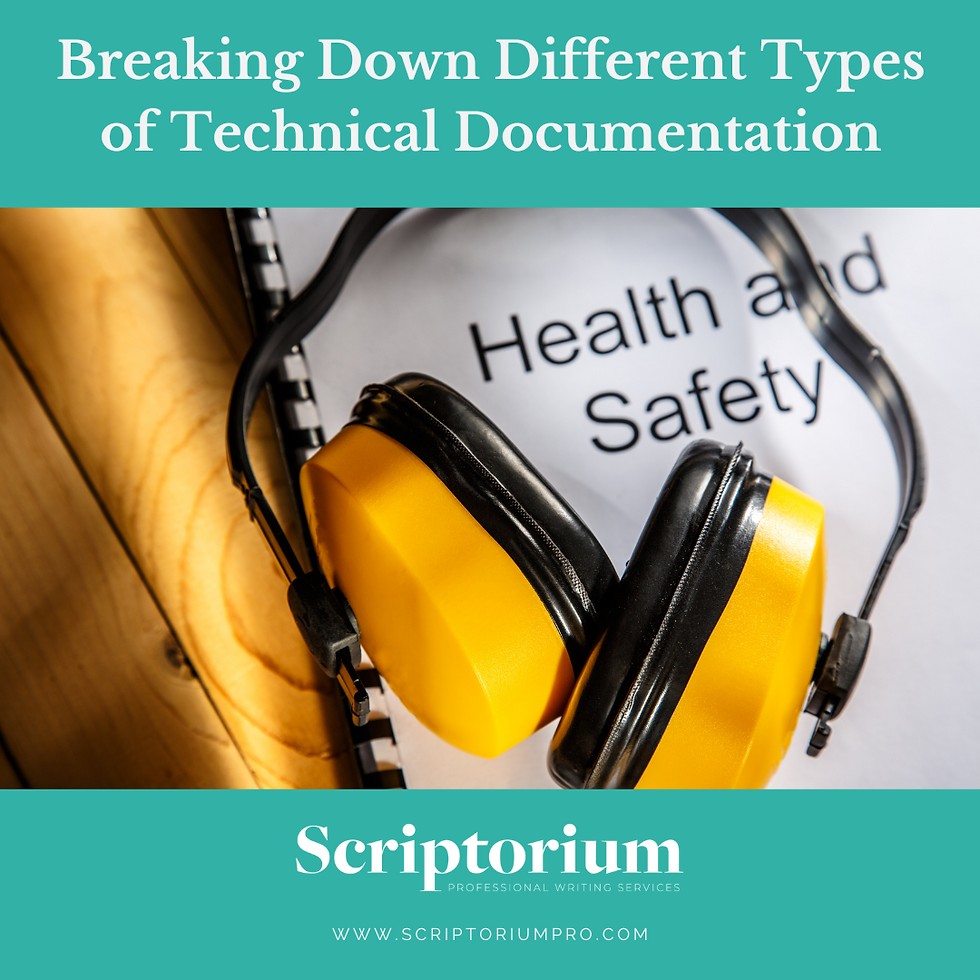
When it comes to technical documentation, understanding the plethora of document types can be daunting. From policies, plans, practices, processes, and procedures as well as hazard assessments and job safety analyses, each document serves a unique purpose in ensuring the safety and well-being of individuals and organizations. Understanding the differences between these documents is crucial in ensuring operational efficiency and safeguarding the well-being of individuals involved with your organization. Let’s explore the key differences between common technical documents and shed light on their distinct purposes and applications.
Policies, Procedures, & Practices
Policies, procedures, and practices can work together to provide different levels of detail and information for an organization’s safety and operations. Ideally, these documents will align and work together to provide standard information for your employees to do work consistently and safely.
Policy
A policy is a set of principles, guidelines, or rules that govern decision-making and actions within an organization or institution. It outlines the intent, values, and expectations regarding a specific issue or area of operations.
Example: Policies often address broad topics, such as health and safety regulations, compliance standards, and organizational values. Often a company’s safety documentation will include a Safety policy that states the organization’s commitment to a safe workplace and defines responsibilities for managers, safety officers, and employees.
Practices
Also known as: Safe Work Practice
Practices are a set of established guidelines or rules that describe the proper and safe way to perform a general task or handle a situation. Safe work practices are broad and cover basic safety principles that apply across various jobs or work environments.
Example: Safety practices could include lifting heavy objects, wearing Personal Protective Equipment (PPE), working at heights, or working in extreme cold or hot conditions.
Procedures
Also known as: Safe Work Procedure, Safe Job Procedure, and Standard Operating Procedure
Procedures are detailed step-by-step instructions for carrying out a specific job or task safely from start to finish. It outlines each step's sequential steps, hazards, and control measures. Unlike policies, which are broad in scope, procedures provide specific, standardized guidance for accomplishing a task. Procedures typically include sequential steps, safety precautions, and troubleshooting tips to ensure consistency and reliability.
Example: Procedures can include any range of specific tasks, such as installing Microsoft software on company computers, changing the engine on a vehicle, or running monthly invoices.
Hazard Assessment & Job Safety Analysis
These documents are proactive tools used to identify potential hazards. They play a critical role in preventing accidents and injuries by systematically addressing workplace hazards. They are completed once and only updated if there is a change in procedure or equipment or after an annual review.
This is a bit of a tricky combo because these terms are often used interchangeably; however, there is a subtle difference: Job Safety Analysis (JSA) focuses on a specific task while Hazard Assessments (HA) can include equipment, materials, locations, and tasks. It is important to align your use of the terms with how your workplace uses them. Consistency with your team will outweigh subtleties in general usage.

Job Safety Analysis
Also known as: Job Hazard Analysis (JHA)
When you do a JSA, you will:
Break down the task into steps.
Identify potential hazards for each step.
Evaluate the severity and likelihood of each hazard.
Develop control measures to eliminate or minimize risks.
Example:
When you create a JSA to change a tire on a vehicle, you would do a step-by-step analysis of potential hazards and ways to prevent or mitigate those hazards. For example, when you jack up the car, there is a risk of the car falling off the jack. To mitigate this potential hazard, you could use a jack stand and double-check to confirm the jack is properly situated before raising the vehicle with the jack.
Hazard Assessment
Also known as: Hazard Identification and Assessment
When you do a HA, you will look at the workplace more generally:
Identify potential hazards in the environment, equipment, and materials.
Evaluate the severity and likelihood of each hazard.
Develop control measures to eliminate or minimize risks.
Example:
When you do a HA for a client worksite, you would review the site as a whole and look for:
● Environmental hazards, such as overhead power lines or flow of traffic;
● Physical hazards, such as working at heights or potential tripping hazards; and
● Material hazards such as propane tanks on site.
Your assessment would also assess potential ways to control or mitigate the hazards. Controls for working at heights could include barriers, such as handrails or using safety harnesses.
Not all companies will require these types of documentation. They may also develop company-specific terminology that is meaningful to their industry and their team. The most important part of developing accurate technical documentation for your organization is to be consistent with how you use the terms and to create templates to provide standard information. This provides a solid foundation to create or update your documentation.
Not sure where to start? Scriptorium can help you develop a plan, create templates, and manage the development of new or updated documentation. Contact us to get started.
#TechnicalDocumentation#YEGCommunications#TechnicalWriting#HealthandSafety#OH&S
#IndustryDocumentation#TeamWork
Comments